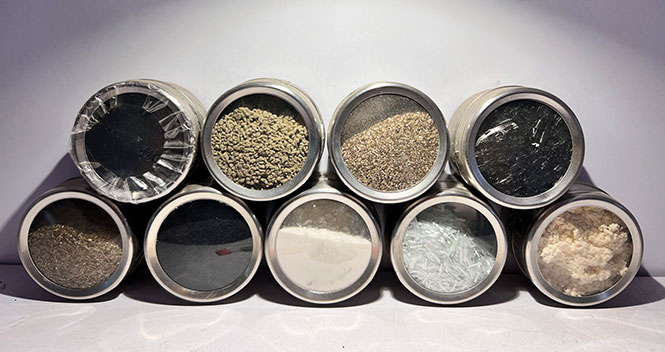
The Performance of the brake lining depends on the science underlying the type of raw materials and the proportion in which they are combined to create a friction product extensive testing in the lab, on the test track, and on the highway is necessary to find the ideal balance between a lining’s strength, Longevity, heat resistance, brake pads and of course cost.
To understand how to assess and compare the quality/ value of a brake lining, we have to look into its formulation. In other words, examine the raw materials used in the friction formula.
Phenolic Resin
Phenolic resin is one of the leading lights of any friction material. This raw material is used as a binding agent, it is cured using a high-heat thermoset reaction. As a result, linings with increased phenolic resin content last longer while maintaining strength and integrity. It also enhances lining wear and life at low temperatures.
Fiberglass
Glass fibres have been considered as a reinforcing agent in friction linings as one component of a potential substitute for asbestos. The use of alkaline-resistant glass fibre in the friction material makes it less susceptible to cracks and prevents chipping. It is cost effective and has superior strength-to-weight ratio.
Abrasive (Aluminium Oxide)
and chopped fiberglass strands are two other essential raw ingredients. Fiberglass improves flexural strength, thus reducing cracking. While abrasives like aluminum oxide create torque when brake lining is used during a stop.
Graphite
Graphite is used as a lubricant in the lining and reduces wear while stabilizing friction levels. Based on the application of the lining, several mixtures or forms of graphite may be used in the formulation of organic materials such as rubber, which is frequently made from recycled tire threads, and friction Dust from cashew shells both contribute to the friction’s softness and more compatible nature.
Other organic minerals known as fillers are calcium carbonate, barytes, and Wollastonite these components are extracted straight from the earth and thus require purification.
Friction Dust
CNSL friction particles, sometimes called friction dust, are used in disc pad brakes and drum linings as a stabilizing agent. These particles have a resilient nature which cushions the engaging property of a piece of lining. Friction dust is added to brake linings to modify the frictional and wear properties of brake linings. In addition, they decompose on the surface of a lining at various elevated temperatures which controls the wear and offers a protective device by prohibiting excessive temperature from being developed. The inclusion of friction particles also helps control brake noise.
Aramid Fiber
Aramid fibre is a new type of high-tech synthetic fibre with excellent properties such as ultra-high strength, high modulus, high temperature resistance, acid and alkali resistance, light weight, and long life cycle. It has excellent wear performance, so it is very suitable to be used as a reinforcing fibre in friction materials. It has the advantages of low braking noise, low product density, low hardness, and no damage to the couple during braking.
Rubber
Rubber, typically recycled tire treads, and friction particle derived from cashew shells are both organic materials that help to make the friction softer and more compressible